As part of it’s efforts at reducing it’s CO2 emissions to promote environmental sustainability, the Dangote Cement Company, Obajana, Kogi State says it has introduced cutting edge technology in trapping dust in the production of cement.
The General Manager, Human Resources, Dangote Cement Company Mr Adinoyi Haruna, made the disclosure in his opening remark on Monday July 7, 2023 at A 2 Day Environmental Journalism Workshop with the Theme; Reporting The Environment For Sustainability, holding at the Dangote Academy, Obajana, Kogi State.
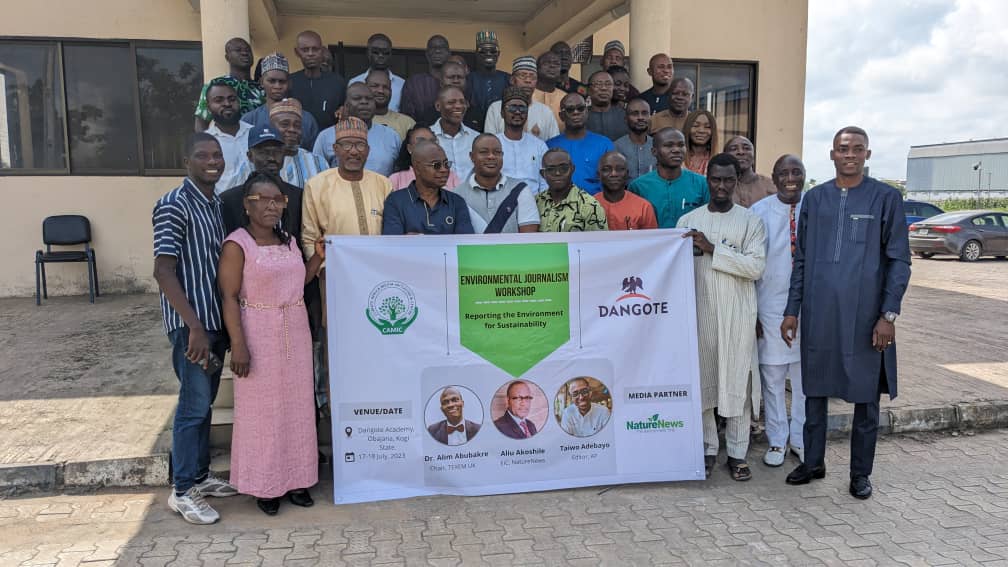
He said the company as part of it’s contribution at reducing emission from it’s plant geared towards protecting the environment of the community it’s operating invested heavily in electrostatic precipitators, ESP’s, in handling particulate emissions from cement production.
Haruna added that the Company also uses bag filters to collect cement dust, and uses 85% of limestone in cement production.
He explained that the companies, limestone initiative is geared towards reducing fuel consumption and reduction of carbon dioxide into the environment in the production of Dangote cement.
Mr Haruna further explained that as a conscious effort to protect the environment, the Cement Company has introduced the use of alternative fuel by using agriculture waste, palm kernel shells, shredded tyres as fuel, aimed at reducing carbon dioxide in the environment.
He therefore called or media practitioners to commit themselves to the sustainability of the environment in their reporting as part of a conscious efforts to mitigate against climate change.
What is an Electrostatic Precipitator
An ESP is an air pollution control device that removes fine particulate matter from a gas stream by using the force of an induced electrostatic charge.
It is widely employed in various industries, including cement manufacturing, to control and reduce emissions of particulate matter, such as dust and fly ash.
By utilizing an electrostatic precipitator in cement production, particulate emissions can be significantly reduced, enhancing air quality and minimizing the environmental impact of the cement manufacturing process.
ESPs can effectively capture and remove a high percentage of fine particulate matter, even particles as small as a few micrometers in diameter.
However, it’s important to note that ESPs are primarily designed to handle particulate matter and may not be as efficient in removing gaseous pollutants.
It’s worth mentioning that there are also other technologies available for handling particulate emissions from cement production, such as fabric filters (baghouses) and wet scrubbers, each with its own advantages and limitations.
The selection of the most suitable technology depends on various factors, including the specific characteristics of the particulate emissions, process conditions, and regulatory requirements.
Environmental Sustainability
Environmental sustainability has become a significant concern across industries, including cement production, due to the high carbon footprint associated with the manufacturing process. Cement production is known to generate substantial greenhouse gas emissions, primarily carbon dioxide (CO2).
To mitigate these emissions and promote sustainability, many cement manufacturers worldwide have been adopting various measures and technologies. These can include:
Energy efficiency improvements: Cement plants can optimize their energy consumption by implementing energy-efficient technologies and practices, such as waste heat recovery systems, fuel switching, and process optimization.
Alternative fuels and raw materials: Incorporating alternative fuels and raw materials in cement production can reduce reliance on fossil fuels and lower CO2 emissions. Examples of alternative fuels include biomass, municipal solid waste, and used tires.
Carbon capture and storage (CCS): CCS technologies can capture CO2 emissions from cement plants and store them underground or utilize them for other purposes, preventing them from being released into the atmosphere.
Use of additives and blended cements: Adding certain materials or blending cement with supplementary cementitious materials (SCMs) like fly ash, slag, or silica fume can reduce the clinker content in cement production. This reduces CO2 emissions as clinker production is a major source of emissions in cement manufacturing.